As the numbers of elevated-temperatures sites grow and research begins to explain why, landfill managers increasingly are turning to specialty-materials piston-pumping systems to reduce incapacitating temperatures.
By Mark Bertane
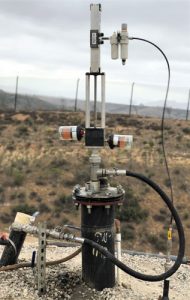
For the past several years, a growing number of landfill managers have confronted temperatures ranging from 150°F to 250°F or more from deep insider larger, wetter, maturing sites—not from subsurface fires, but from biological or chemical exothermic reactions within the zones of the landfill itself.
High concentrations of varied, recombinant leachate compositions in these Elevated Temperature Landfills (ETLFs) can lead to higher costs for treatment or even the refusal of local wastewater treatment plants to accept the leachate, according to an industry journal.1
Elevated temperatures may also result in slope instability due to reduced waste strength or increased liquid- or gas-pore pressures, surprise sinkholes and rapid settlement—all safety and infrastructure issues.
In addition, odor and the possibility of offsite gas migration and leachate release have resulted in public demands for tighter operations and oversight and, occasionally, litigation. Research into the causes and spread of ETLFs is ongoing.
Equipment Failures
ETLF events pose a significant threat to existing leachate and gas-well physical systems, including commonly used educator/riser piping, tubing and pumps that were not designed for high-temperature use.
Heat tolerance for nylon tubing and/or HDPE pipe or tubing.is generally rated at 150°F (66 C°), a temperature at which air-push pump models also begin to struggle. If temperatures exceed 150°F, plastic piping often becomes elastic and standard air-push pumps are prone to failure—gas-well systems can be compromised and leachate pumping halted. At this point, the site is in danger of becoming an ETLF.
Why Temperatures Rise
More sophisticated metering and monitoring of landfill gases is making it easier to deduce if higher temperatures are caused by subterranean fires (more carbon monoxide present) or bio-chemical reactions (at high temperatures, methane can turn into hydrogen and other gases).
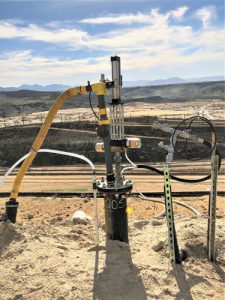
Shown: Blackhawk V-2 ET Pneumatic Piston Pump.
Elevated concentrations of these gases combined with lower levels of methane may indicate the presence of an active bio-chemical condition—an ETLF problem.
Because liquid holds more heat than gas, failure to remove chemically reactive fluid means subsurface crevices generate increasing amounts of heat. The lighter gas, with the capability of dissipating heat far more easily, is forced away, often into open air or offsite, while the heated fluid remains. Absent intervention, the site is in difficulties.
Fighting Back/Getting Out Front
Managers at some of the most challenging ETLFs have developed new strategies and tactics shown to slow and then reverse increases in site temperatures—getting ahead of the problem before a warming site becomes a full-blown ETLF.
If the heat source is exothermic reaction, dewatering is necessary, allowing cooler, lightweight gas to replacing hotter fluid in underground fissures. Over time, as the hotter liquids are pumped out (conduction), more gases are collected and recovered (convection), reducing overall site temperatures—pulling back from the ETLF threshold.
Elevated-Temperature Piston Pumps
Positive-displacement piston pumps are playing a key role in ET dewatering. Unlike common air-drive models, piston pumps can be built with materials of construction that withstand heat to 300°F+ (150°C). They will pump virtually anything flowable, regardless of composition, pH, viscosity, grit or vacuum while resisting biological and chemical attack.
By design, piston pumps cannot introduce oxygen into the discharge system or exhaust landfill gases into the atmosphere. Drivers are mounted above the wellhead, and all power and drive components are above ground for safer and faster maintenance. A site that already has crossed the ETLF threshold generally will require significant changes to its infrastructure components—both pipes and pumps.
In addition to installing elevated-temp pumps, sites must replace stretched or otherwise failed HDPE piping. Discharge pipes must be above grade, and, importantly, must be sized to handle fluid flow, allowing access to clean out scale and other build up. Managers report that steel hard pipe has been a reliable solution.
Reducing Incapacitating Temperatures
As the numbers of elevated-temperatures sites grow and research begins to explain why, landfill managers increasingly are turning to specialty-materials piston-pumping systems to reduce incapacitating temperatures. And, if aggressive LFG well dewatering can reverse warming trends before infrastructure breakdown, the costs can be surprisingly low. | WA
Case Study: A North American ETLF Site
More than a decade ago, a now-closed landfill outside a U.S. city was experiencing a public and legal reaction to increased odor, offsite gas migration and leachate release. The accumulation of altered-chemistry leachate—heavier than gas and changing its composition with age—is now believed to have been the cause, eventually creating a subsurface exothermic reaction over several acres that raised temperatures to an estimated 200°F or more in some zones.
The common air-push pumps onsite were not designed for elevated temperatures—reducing or incapacitating the pumps’ ability to dewater that portion of the landfill. With leachate continuing to accumulate, landfill gas was pushed into the open air, beyond the site’s ability to capture and flare it, and migrated into nearby basements. A court ordered improvement and mandated dewatering of at least 120,000 gallons per month.
Not then knowing the causes of the air-push pump failures, but understanding a new approach was necessary, managers installed several Blackhawk top-head-drive, positive-displacement pneumatic piston pumps in the area where common air-push and submersible models failed.
The Blackhawks notably outperformed the other pump styles, although issues surfaced as more piston pumps were added—including relatively rapid seal wear and field technicians’ unfamiliarity with the new pumps.
So, in the spirit of need and opportunity for growth, the landfill’s management team partnered with Blackhawk to diagnose problems, better understand what was happening at the most challenging wells and then develop new design concepts and test new materials to meet unique needs. Now 10 years later, both the actively managed landfill and Blackhawk have benefitted significantly from the mutual exchange of ideas and continuous onsite proof testing.
At the Landfill
• Liquid levels have been reduced and stabilized below mandated levels in the ET zone.
• Flow rates have increased by more than 15 percent with the addition of steel infrastructure tubing and stainless-steel pump parts.
• ET zone temps have been lowered at least 25 percent to roughly 150°F—still too elevated for common landfill pumps, but low enough to keep gases flowing to the flares.
• At any one time, between 30 and 35 of the original Blackhawk pneumatic piston pumps remain in operation, a result of conscientious maintenance and technician training.
• Most significantly, the site is meeting its court mandates and odors have virtually disappeared.
At Blackhawk
• A new line of piston pumps was developed for ETLFs, both pneumatic and electric powered, with a solar model proposed.
• A variety of stuffing-box designs, components and materials have improved the durability, ease of maintenance and replacement of seals and blocks for all Blackhawk pumps.
• Blackhawk’s now-standard zinc-coated stainless-steel flanged well seal was developed with a unique external stay-clean system.
• All pneumatic tie-rod dimensions were extended to allow greater distance between driver and stuffing box.
• Most significantly, a greater understanding of the nature of ETLFs has helped sites improved the quality of life for neighboring residents.
Mark Bertane is Founder and Principal of Blackhawk Technology Company (Glen Ellyn, IL), a leading provider of piston pumps. Blackhawk is broadly recognized for customer-driven technical innovation and reliability in even the most extreme pumping environments. Mark can be reached at (630) 469-4916, e-mail [email protected] or visit www.blackhawkco.com.
Note
A 3-part series by Waste360 in conjunction with ELEF: www.waste360.com/landfill-operations/diagnosing-and-understanding-elevated-temperature-landfills-part-1.