Dust Control Case Study
When Ahrens Contracting acquired the contract to demolish and remediate a St. Louis Superfund site, they turned to MobyDick to contain the contamination.
When Ahrens Contracting, Inc. accepted the remediation contract for the abandoned Carter Carburetor Site, they found themselves with quite the challenge. Known nationally, with a core market in Missouri and Illinois, Ahrens was taking on a Superfund site in their own backyard: St. Louis. The St. Louis Post-Dispatch called Carter Carburetor “one of the city’s most-polluted industrial properties.”
The Site
Carter Carburetor founded in 1909 and later acquired by American Car and Foundry Company, operated for more than 75 years supplying carburetors for Willy-Overland Jeeps, Chrysler and Buick, and even manufactured competitors’ designs when those companies could not meet demand from GM and European automakers. The plant stopped production in 1984 when the rise of fuel injection decimated the market for carburetors. Unfortunately, Carter’s important and successful legacy also included environmental impacts: the site of the shuttered Carter Carburetor foundry in the JeffVanderLou neighborhood of St. Louis, ultimately, became an EPA Superfund Site. Among other chemical contaminants, polychlorinated biphenyls (PCBs) and trichloroethylene (TCE) impacted the soil and ACM was found in the buildings.
HRP Associates, Inc. (HRP), the engineering company of record for the Carter Site, has been providing the Project Management, Construction Management and Environmental/Civil Engineering Services required to direct operations the Carter Carburetor Site. HRP is a multidisciplinary environmental/civil engineering consulting firm with office locations throughout the U.S. and Global Consulting Services, which extends to more than 20 countries throughout the Americas, Europe, and Asia. The Carter Carburetor Site is privately funded under two Administrative Orders of Consent: an Engineering Evaluation/Cost Analysis (EE/CA) and Removal Action(s) (which is currently underway) at the former 10-acre industrial site which was comprised of a 450,000-SF, four-story manufacturing facility and associated warehouses, buildings, parking lots and former sites of underground storage tanks.
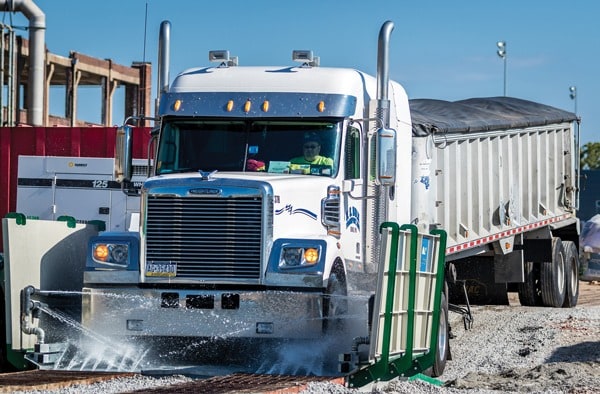
Photo courtesy of Gene Watson.
Ahrens Contracting, Inc.
Locally headquartered firm Ahrens Contracting, Inc. acquired the contract to demolish and remediate the Carter Carburetor Site. Founded in 1983, Ahrens specializes in excavation, demolition, site recycling and environmental remediation for industrial, commercial, residential and government customers. Employing approximately 65 full-time employees, the company generates $15 to $20 million worth of business each year in greater St. Louis, Missouri, Illinois, and across the nation. Ahrens recently traveled as far as Tucson, Arizona to complete the demilitarization and scrapping of F14 fighter jets at Davis-Monthan Air Force Base, the final resting place of all U.S. military and government aircraft. Ahrens Contracting, Inc. is also a proudly certified woman-owned business: President/CEO and owner Patricia Ahrens is a long-standing member of the National Association of Women in Construction.
Suppressing Dust and Contamination
Work on a Superfund remediation is in many ways different from a standard demolition, cleanup and recycling. Factors, such as control of track out and suppression of fugitive dust, that on a normal job might simply be a case of compliance or neighborly good conduct, are public health and safety imperatives when dealing with the level of contamination of a site like Carter Carburetor. Vehicles exiting the established “exclusion zone” must be decontaminated by a well-defined EPA procedure. Air, water and soil sampling are conducted on and around the site over the course of the project in order to ensure that no contaminated fugitive dust, soil or water has escaped. In addition to issues inherent to a Superfund site, Ahrens had to contend with the variable St. Louis weather. Ted Ahrens, purchasing agent and assistant project manager for the Carter Carburetor Site, described conditions ranging from freezing rain, ice and snow, to extreme heat that saw work cut to half-days for the safety of workers. Ted Ahrens also describes “gully-washers” that required the company to spend multiple days pumping out open excavations (and handling that now-contaminated water) before work could resume. Dust control was also a particular challenge on this project. In addition to dust generated during the buildings demolition, part of the process implemented by Ahrens involved crushing and recycling the existing concrete onsite, totaling almost 600,000 sq. ft. The recycled concrete was used as fill for the significant quantity of extremely contaminated soil that was removed from the site and shipped by rail to be landfilled out of state. Through it all, however, Ted Ahrens said the company’s choice of the MobyDick equipment was a great asset to achieving Ahrens’ objectives “that no project dirt or dust gets past the fence. The wheelwash was the last stop. The roads were kept clean.” The MobyDick dust control cannons “worked out really well containing the demolition and the concrete recycling crushing generated dust. Our operators really liked the wireless automated controls.”
MobyDick
Photo courtesy of Mike Whitney.
FRUTIGER Company AG has been combatting dust and track-out problems for almost 60 years. Recently, the company has expanded its portfolio of market-leading MobyDick-brand wheelwashing systems, providing proven wheel and undercarriage washing and demucking through more than 4,000 installed systems worldwide, with the addition of a new line of dust control cannons that aim to bring the same level of quality and durability to airborne dust suppression.
FRUTIGER Company AG has 150 Employees and an annual turnover of $50 million. FRUTIGER factories are ISO 9001 2009 certified.
The Carter Carburetor Site is in a residential area of St. Louis, and as part of the Scope of the Project, Ahrens needed to ensure no chemicals of concern left the Site on the wheels or chassis of trucks exiting the site. A simple knock-off grate might have removed some of the caked mud from the tires, but the truck would still require a thorough manual cleaning before being permitted outside the exclusion zone. The MobyDick ConLine Model 400MC surface mounted wheelwash system that Ahrens purchased automates that process. “The faster solution was a boon,” said Ted Ahrens. “It saves us overhead on cleaning tires, and is safer for laborers than holding a fire hose.” He added, “It frees (them)up for other work.” Also important to Ahrens was the ease of assembly, use and factory support, “The MobyDick tire wash was assembled in two days. MobyDick sent a field service technician on site to supervise, train and assist.”
As the project outgrew Ahrens’ existing fleet of dust control cannons, the company again reached out to Frutiger to acquire two of the new MobyDick Dust Control Cannons. When asked why his company chose cannons from MobyDick, a relative newcomer in the dust control sector in the U.S. after years as a wheel washing leader, Ted Ahrens tagged a key feature of the product, “Automatic cannons with (wireless) remote control lets laborers and operators stand safely back from the demolition. Equipment operators like being able to move them from within the cab to handle rapidly changing wind conditions and work at varying elevations.”
He also praised MobyDick as a whole, citing a high level of satisfaction with his company’s MobyDick ConLine as a factor in Ahrens’ purchase of the dust control cannons. “We had good results with the tire wash,” he says, “It’s nice to deal with one company that can offer multiple products and stand behind those products. The MobyDick Dust Control Cannon performs very well.”
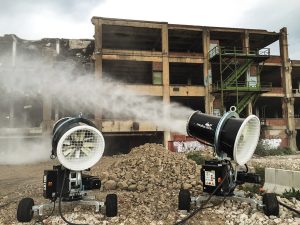
dust particles to the ground. Options shown lifting rings, water shutdown valve, wheel set.
Photo courtesy of Mike Whitney.
Unique Issues, Solved
MobyDick prides itself on the water-recycling prowess of the ConLine series of systems, but at Carter Carburetor the efficient collection of wash water proved useful in a different way. Rather than directing the captured water back to the high-powered ConLine pumps to be reused, as is the standard installation profile, Ahrens routed the used wash water to a grid of seven 16 to 22,000 -gallon fracking water tanks, where the contractor stored the water for decontamination as per EPA guidelines. Once properly treated and tested, the water could be discharged safely. The design of the MobyDick system allowed virtually all of the used water to be captured and treated, minimizing further contamination of the site.
A Successful Endeavor
As of the beginning of July 2016, after 11 months of work, the Carter Carburetor project stands approximately 97 percent complete. Ted Ahrens reports that the company is awaiting some final Site sampling before putting the finishing touches on the job. When asked about the performance of Ahrens Contracting’s MobyDick equipment, Ted Ahrens reiterated the importance and convenience of a single supplier of quality equipment, and said, “everything worked to its full potential.”
He added that since the start of the Carter Carburetor job, the company has purchased another MobyDick ConLine unit: “The MobyDick worked so well at the Carter project, we purchased another MobyDick (ConLine Model 400MC) system for an Illinois chemical plant demolition project. The MobyDick was fairly easy to put together; we put the second system together ourselves.” Asked if the company would continue using MobyDick products on future jobs, Ted Ahrens said the company would definitely “take these to other jobs” and look into acquiring more in the future.
Benjamin Lodi is a technology and marketing consultant for MobyDick and FRUTIGER Company AG based in Pittsburgh, PA. He can be reached at [email protected]. For more information, visit www.mobydick.com MobyDick equipment rental is available through Rain For Rent at www.rainforrent.com.
*Gene Watson, Regional Office Manager for the HRP Associates, Inc. St. Louis, MO branch, is the Project Manager/Project Coordinator for the Carter Carburetor Superfund Site. He took the photos included in this article with a Canon 7D Mark II with various Canon L Series Lenses. He can be reached at [email protected].