Ergonomics is the study of the interactions between workers and the tools and equipment used to perform jobs. In the case of the waste collection, ergonomics focus on the driver, his or her truck, and the tools, equipment, and process used to complete a route. Understanding employee interaction with tools and equipment provides valuable insight that can be used to protect workers better design, engineering, and operations.
By Will Flower
People in the waste and recycling industry are tough. All day long, drivers and helpers routinely lift trash cans, recycling bins, and bags. At landfills, workers unload and compact waste. At material recovery facilities, workers sort and segregate tons of materials for recycling. However, even the strongest worker can be injured by overreaching, improperly lifting, or working with poorly designed tools or systems.
Back strain and muscle sprain are the most common type of injury facing workers who collect and process wastes and recyclables. However, other injuries include musculoskeletal disorders such as tendinitis, carpal tunnel syndrome, and rotator cuff injuries. All of these injuries can be extremely painful and result in lost time and visits to doctors.
The good news is that many injuries are preventable by examining and changing workspaces, work techniques, and modifying tools used to do a job. Employees can be provided with additional protective equipment. Tools can be upgraded. Work techniques can be altered. Workspaces at recycling centers can be adjusted.
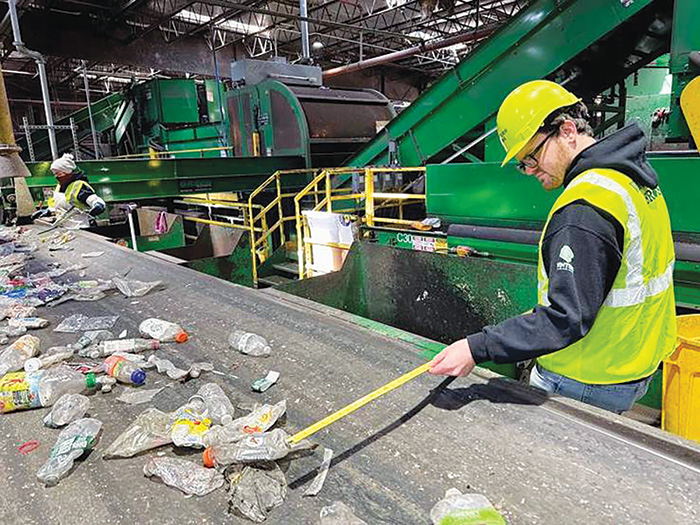
Improving Safety
To start the process of using ergonomics to improve safety, general managers and safety professionals should follow these steps:
1. Review the history of workplace injuries: Collect and analyze health and injury records to evaluate and determine if there are specific jobs or activities that result in repeated injuries. Identify the root cause of repeated injuries.
2. Identify risks: Evaluate the workstation layouts and standard operation procedures. Talk to drivers and laborers to solicit their input about the workspace, work processes, job tasks, and equipment. Identify risks that can lead to stains, sprains, and other musculoskeletal injuries.
3. Education and training: Review best practices with managers and workers. Make sure everyone understands the importance of using personal protective equipment. Employees who work with tools and heavy-duty equipment must understand and follow proper operating guidelines.
4. Implement your ergonomic program: Make adjustments to improve safety. This can include changing job techniques, workstation layouts, and processes to make the interaction between workers and machines less stressful. Engineers at equipment manufacturers can be instrumental to making improvements.
5. Continuous improvement: The management team and workforce must be steadfast in their commitment to continuous improvement. Regular reviews and inspections of workplaces and workstations should be completed. Keeping workers involved in the evaluation process is important.
6. Evaluate new equipment and systems: Facility managers will want to have a high level of confidence that the new sorting system or process is safe for employees. Any time a new collection truck, new processing systems, or new tool is introduced to the workplace, the equipment should be evaluated for acceptable ergonomics. Every employee working at the facility should be educated about the proper use of the new equipment. Training should also cover the necessary personal protective equipment and Lock Out/Tag Out procedures to keep employees safe when repairing or cleaning a machine. A pre-startup safety review should include an examination of the entire facility with a close look at the equipment that was modified or upgraded. Safety professionals and managers should make sure that all equipment was properly installed in accordance with design and manufacturer’s specifications. Ergonomics should be one of the items that is reviewed prior to starting up a new piece of equipment. Other items to review include electrical connections, guarding around chains, belts, gears, pulleys and motors, proper lighting, noise hazards and fire hazards.
7. Care for the injured: Good healthcare and Return-to-Work programs will help injured employees get better and return to a safe work environment.
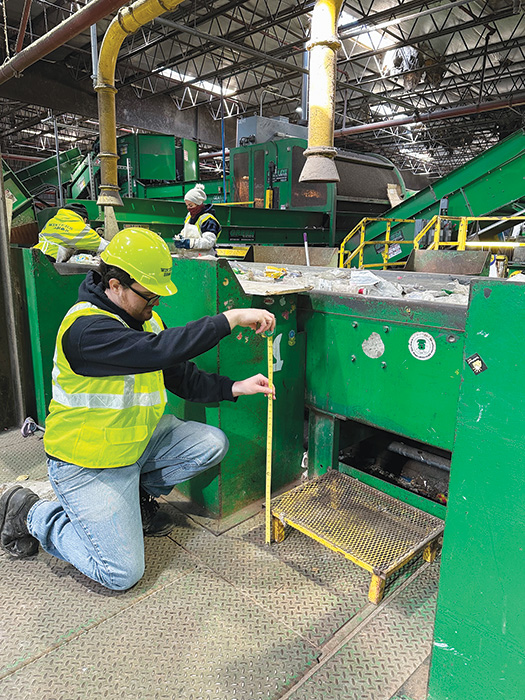
Avoiding Strains and Sprains
Injuries to employees are costly and can significantly reduce worker productivity and morale. To protect workers, safety professionals should regularly discuss the precautions to take to protect their muscles and backs. Drivers and laborers working on collection routes should consider these tips for avoiding strains and sprains:
• Stretch and warm up. The work is physically demanding, and muscles should be properly stretched and warmed up prior to lifting heavy loads.
• Wear proper shoes and gloves. Sturdy shoes will provide good footing while good gloves will provide grip when you lift.
• Before lifting a waste container, move it slightly to gauge the weight. Remember, you cannot judge the weight of a container by looking at it. While one residential container may be light, the next one could be super heavy.
• Survey the area to make sure the walking surface is free of trip and slip hazards.
• Grip the object firmly.
• Lift properly and slowly, with knees bent and back straight.
• Let the legs do the lifting.
• Avoid twisting your body.
Focus on Safety Measures
In the waste and recycling industry, the significance of ergonomics and safety cannot be overstated. Workers engage in physically demanding tasks, such as lifting heavy materials, operating machinery, and navigating potentially hazardous environments. Implementing ergonomic principles is crucial to ensure the well-being of workers, as it helps reduce the risk of musculoskeletal disorders and injuries associated with repetitive or strenuous activities.
A focus on safety measures is paramount to safeguard employees from potential accidents. Training, proper equipment, and ergonomic design of workspaces contribute to a safer work environment. By prioritizing ergonomics and safety, not only can the waste and recycling industry protect the health and productivity of its workforce, but it also promotes a culture of responsibility, ultimately enhancing the overall efficiency and safety of the waste management process. | WA
Will Flower is the Senior Vice President of Corporate and Public Affairs at Winters Bros. Waste Systems on Long Island, NY.
Share your safety tip. Submit your suggestions to Will Flower at [email protected].