Excellent planning and strategic design can save you money and time in the long run.
By Audrey Brewer
Designing a shredding system for the waste-to-energy market is an enormous undertaking, one that requires significant planning. But with booming populations and an excess of waste going to landfills, this industry is growing at a rate that cannot be ignored.
The best way to keep municipal solid waste out of landfills is to process them in a plant that is able to turn waste into Alternative Fuels/Refuse Derived Fuel (RDF.) Here are some things to consider when it comes to shredding.
#1: Work Your Way Backwards
Though a shredder will go more toward the beginning of a waste recycling line, it’s imperative to consider the end goal first. Knowing your end user and what product they are capable of purchasing from you is a great first step. This allows you to sort out metals, PVC or organics should they want those sorted out of the product. If this is the case, the layout of the plant will have to be adjusted to include metal detectors to prevent large metal objects from entering the system, magnets to eliminate ferrous metals from the waste stream, eddy current separators to eliminate non-ferrous metals, density separators and screens to remove organics such as food waste. Optics can also be installed along various conveyors to withdraw PVC and any other unwanted non-metal item pieces on either side of the pre-shredder.
All in all, the end product drives the plant’s entire design. It’s important to see the big picture before you get down to the nitty gritty, and to lay the plant out accordingly.
#2: Prevent Prohibited Objects from Entering the Waste Stream
The sorting process before the waste stream even reaches the shredder is of the utmost importance. This can be done manually using a front-end operator sorting through the material, or by hand using a sorting belt. There is also an automated way to tackle the daunting task of pre-sorting materials, including metal detection and/or a system infeed conveyor using optics or metal detection that is designed to stop the belt in the instance of prohibited material. Knowing your end user allows you to set up these pre-sorting methods in a way that will most effectively and efficiently keep your waste stream clean.
#3: Allot Time for Downtime
It is imperative for shredders to be maintained regularly, especially within the waste industry, where a variety of materials is introduced into the shredder and processed at once. The best thing you can do for your operation to prevent large chunks of down time is to routinely and thoroughly clean and maintain the shredding chamber. Turning knives and replacing counter knives regularly is important to keep the cutters sharp and performing optimally. One severely damaged knife can shut down a whole system if not dealt with proactively. Checking belts for wear and replacing them if necessary can also prevent any unwelcome surprises while the shredder is in operation.
The most important thing is this: hindsight is 20/20, and foresight is priceless. Excellent planning and a strategic design can save you money and time in the long run—two things that, unlike waste, are not in infinite supply. The waste-to-energy market is a growing one, especially as green technology improves. These methods of incorporating shredders into your production line will set you up for success in an industry that demands strategic solutions and can have a big impact on both the environment and your bottom line. | WA
Audrey Brewer is the Marketing Manager for WEIMA America (Fort Mill, SC). Through her time at WEIMA, she has come to see the value of green technology in a world that is ever-changing and whose resources are in short supply. Her goal is to see companies become more profitable through renewable energy sources. She can be reached at [email protected].
CASE STUDY
In an attempt to cover the demand for cement and simultaneously save energy and production costs, a decision was made in Bogor to use replacement combustible produced in-house instead of fossil resources to supply the vast pre-heaters and rotary kilns.
Supplied industrial and domestic waste was directly input to the two WEIMA PreCut 2000 primary shredders using front loaders. The robust drive enabled extremely high torque values at a low kW output. The screen below the rotor ensured a homogenous shred size.
After primary shredding, the material flow was separated and sorted into heavy, moderately heavy and light fractions. For this purpose, the system applied an Ecostar Dynamic Screen, a Westeria windsifter and Steinert magnetic drums, all of which are linked by Westeria conveyor belt technology. As a result, the system ensured that no foreign material, such as stones or metal objects, could penetrate into the two WEIMA FineCut 2500 secondary shredders.
Finally, a discharge conveyor belt transported the material from the secondary shredder to an adjacent warehouse designed as a temporary buffer. From there, it was removed to ultimately fulfill its purpose as valuable combustible material for calcination.
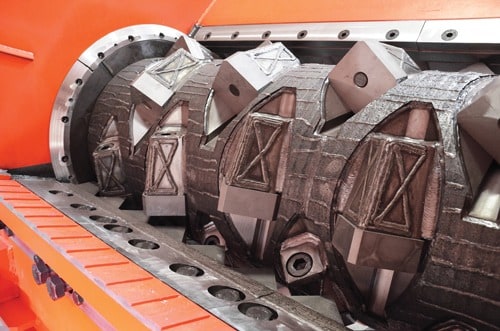