Rigid-frame fabric buildings hold the key to optimized facility solutions for waste applications.
By Matt VanScoyoc
Waste industry facilities come in many shapes and sizes due to the extremely wide array of applications to which they must cater. From material recovery facilities and transfer
locations, to pump stations and wastewater treatment plants, to compost covers and biocycle centers, professionals working in different corners of the industry have their own unique sets of concerns.
What they have in common, however, is the challenge of dealing with materials that typically create messy, smelly and even corrosive environments. The corrosion factor, in particular, is a central reason why tension fabric structures—characterized by their fabric membrane cladding for roofs and sidewalls—have cemented themselves as an effective solution for waste-related building needs.
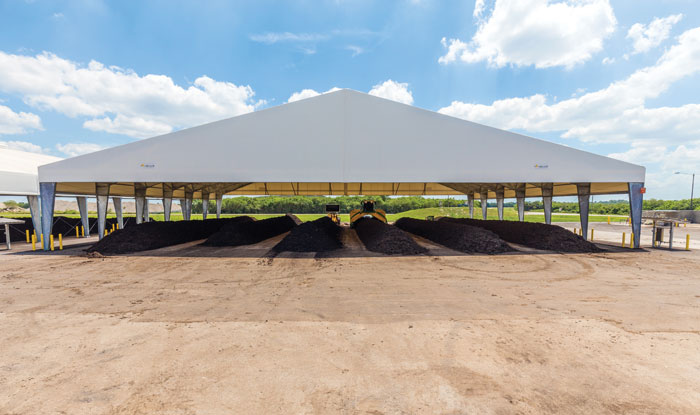
Solid Solution
Fabric buildings historically have been synonymous with “hoop structures” in the waste industry and elsewhere. However, the fact is that many modern fabric-covered buildings bear no resemblance to those flawed hoop designs, instead delivering a conventional construction approach in combination with fabric’s various architectural advantages.
More than 10 years ago, rigid-frame metal-building engineering was introduced to the fabric structure market1 with the goal of bringing a higher level of engineering integrity. Where traditional hollow-tube, open web truss framing had led to notoriously subjective evaluations of fabric structure designs, the use of rigid frame I-beams was proven and universal, making it far easier for all aspects of a building project to be understood by everyone involved.
Steel I-beams are obviously thicker and more durable than hollow tubes, but their primary strength from an engineering standpoint is design flexibility. Rather than being forced into a standard size building offering, as was typically the case with most web-truss fabric building suppliers, users can take advantage of the rigid-frame approach to customize the building layout and dimensions to most logically fit their operation.
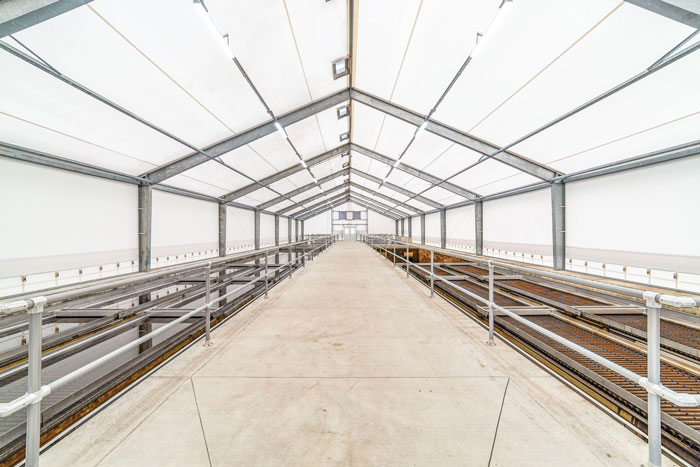
resistance.
For example, waste collection or processing facilities will often have trucks, trailers and other equipment tipping and dumping loads inside a certain section of a building. A rigid-frame structure can easily be designed from the beginning to provide ample ceiling clearances in an unloading area, without necessarily having to do the same for the entire structure.
An additional benefit of using solid steel beams is that the building will have straight sidewalls like any conventional structure. Older-style hoop buildings have curved or rounded frames that do not allow enough clearance for activity near the sidewalls. Straight sidewalls effectively maximize the available square footage of the building footprint.
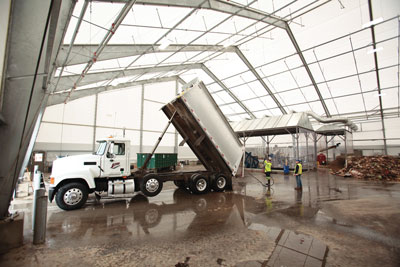
clearances in an unloading area, without having to over-engineer the entire structure.
Longevity with Epoxy
Another problem with traditional hollow-tube frames was that corrosion could actually originate inside the tubes, sight unseen, and eat away at the tubes from the inside out. Although I-beams are completely solid steel, even they need some added protection from prolonged exposure to the caustic environments created by many waste industry applications.
Galvanizing, and hot-dip galvanizing in particular, has been a popular standard for treating a structural frame and other steel components. This approach has had success, but it does come with a limited service life. Galvanization adds an ASTM A123 average layer of 3.9 mils of zinc that is vulnerable to degradation. It may be very effective for 15 years in a high-humidity or caustic setting, but eventually the coating will give way and the frame itself will begin to corrode, leaving limited options for remediation.
Recently, manufacturers have introduced epoxy paint, thereby providing a treatment coating that creates an actual barrier between corrosion and the steel member. Instead of only slowing the corrosion process like galvanizing, epoxy puts a barrier between the corrosive elements and the steel, making it a true preventive maintenance measure that adds many years of longevity to a building’s lifecycle.
Furthermore, from an ongoing maintenance standpoint, it is easy to repair an epoxy-coated steel member if it were to be dinged or scratched by equipment or vehicles. Any affected areas of an I-beam, or any coated steel member, can be blasted and re-coated with epoxy if necessary.
The Beauty of Fabric
While some sort of treatment is generally required to protect steel framing and components from corrosion, no such protection is needed for fabric cladding itself, due to its inherent corrosion resistance. It is easy to understand why fabric is used in many waste facilities, and the available materials continue to improve.
Most industries traditionally relied on polyethylene (PE) fabrics, while polyvinyl chloride (PVC) fabric was commonly reserved for higher-end projects due to its higher cost. However, some PVC offerings have now become available at comparable price points to PE, making it possible to extend the life expectancy of a fabric roof without having to invest any more in a project.2
PVC and PE fabrics are both translucent materials, allowing natural light to illuminate facilities during daylight hours. In many applications this capability either reduces or eliminates the need for artificial lighting, helping to cut electric bills in either case. Additionally, fabric’s properties related to thermal emittance and solar reflectance commonly help keep building interiors warmer in the winter and cooler in the summer months.
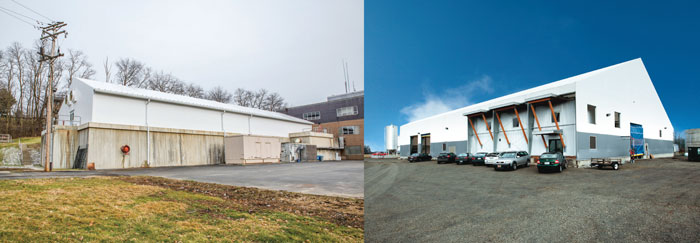
Right: The structural I-beam engineering approach allows users to customize
a fabric building layout and dimensions to most logically fit their
operation.
Breath of Fresh Air
Water treatment plants and solid waste collection stations are among the many building applications that will naturally have to deal with noxious odors. Whether the concern is alleviating hazardous gas emissions to keep the environment safe for workers, filtering out corrosive elements or simply reducing the degree to which foul odors persist, ventilation is obviously important.
Composting and bio-cake storage buildings are often built to function mostly as a cover, allowing for outdoor breezes to help clear fumes, promote air movement for accelerating the process and protect windrows or piles from moisture.
Other times, perhaps due to location and feedstock, a structure may need to be airtight to contain and capture aromas, which are then scrubbed and processed through air-handling equipment before being released. In contrast to metal structures, which are assembled with screws that cause penetrations where air leaks can occur, leading fabric buildings have been pressure-tested and found to have a much tighter envelope—leading to less leakage, increased optimization of air-handling equipment, and lower operating expenses.
Alternatively, passive ventilation systems, a standard feature on some rigid-frame building designs, rely on the simple movement of warm air. Ridge and soffit vents draw air into the structure and circulate air out. This passive process is sufficient to handle the humidity and moisture concerns of most facilities, saving entities on both the purchase of a mechanical system and the ongoing costs to operate it.
Put a Load On
For instances where mechanical ventilation means are required, such systems can be mounted onto the structural frame. The rigid-frame concept allows designers to modify each individual I-beam or add support framing, as necessary, to account for any desired loads and stresses. This approach provides optimal engineering value, putting more strength precisely where needed and applicable, rather than over-engineering the building and adding unnecessary, and perhaps impractical, material cost.
The same goes for any hanging or collateral load required for a waste building. Material recovery facilities can include mezzanines or catwalks to oversee operations taking place. Conveyors, cranes, fire suppression systems or other mechanical equipment can likewise be suspended from the ceiling, provided the structural framing has been engineered to handle those loads from the start.
Cost-Effective Buildings
It is worth reiterating the high level of flexibility available to users. Because each rigid-frame fabric building project begins with a clean sheet, any and all needs can be addressed. Operators investigating cast-in-place concrete retaining walls for holding material can often save money by instead setting precast panels inside a structure with fabric sidewalls. Buildings can include long clear spans, lean-tos, offset peaks, sidewall doors or any other feature. In short, users can get a cost-effective building that is
completely optimized to their function. | WA
Rigid Frame in Practice
As part of the upgrade of their Fern Hollow water treatment facility, Moon Township, PA, decided to enclose the clarifying equipment in a fabric building. “Having a building protects the tanks,” said Burt Rateau, Water Treatment Superintendent at Moon Township. “Ducks can’t land in it, it keeps the leaves out, the building keeps the bug population down and controls algae growth, and you can’t throw things in the tanks.”
After researching many building options including steel, brick, tin and concrete block, the team ultimately decided that a fabric structure from Legacy Building Solutions would best meet their needs. In particular,
Legacy would be able to design and install a rigid-frame building around the facility’s existing tank footprint and varying wall elevations.
“It’s a neat-looking building,” said Rateau. “We’re in a residential area, so we try to be aesthetically pleasing. And the upkeep seems easier—no worries about windows leaking or cracks in the brick.” The building is clad in white ExxoTec fabric. The fabric transmits visible light while blocking and reflecting ultraviolet rays, which prevents algae growth.
Ventilation was another concern inside the building. The finished design incorporates a passive system consisting of overhangs with mesh-ventilated soffits and framed louvers for air intake along with ridge vents for exhaust, as well as an active system using fiberglass fans that provide the air circulation needed inside to control humidity and mitigate moisture-induced maintenance.
Legacy’s in-house crews installed the building overtop the existing water treatment equipment. Installation was completed in only 14 days. “A brick building would have taken months and probably been triple the cost,” said Rateau.
As part of an expansion project, the Lee County Solid Waste Division added three pavilion-style fabric structures from Legacy Building Solutions to an existing facility in Felda, FL. “Adding the three buildings almost doubled our production space, including capacity for blending feedstocks and building rows,” said Keith Howard, Deputy Director of the Lee County Division of Solid Waste. “It increased our throughput of biosolids to close to 50,000 wet tons per year.”
Each building houses six windrows of compost. The windrows are created with a front end loader and turned regularly by a specialty grinder, making tall clearances essential for business. Thanks to the I-beam framing, loaders can be driven right up near the walls with room to maneuver. The facility’s other structures each have six to eight feet of space on the sides that are not accessible with a loader because trusses are in the way.
Moisture control is another critical factor when processing compost. The fabric buildings have enclosed gabled ends to limit the amount of precipitation coming inside, but walls are left open to an extent to allow maximum airflow. Each building’s steel frame system also supports two large ceiling fans, as well as ridge vents to exhaust stale air and odors out the top of the structure.
The PVC fabric used for the buildings included an acrylic coating and is flame-retardant and specially designed to withstand exposure to harsh ultraviolet rays. The strong solid frame design provides greater wind resistance than Lee County’s original buildings, allowing them to withstand ultimate wind speeds of 150 miles per hour. They also meet seismic “A” and standard hazard design codes.
Matt VanScoyoc is a Building and Project Design Consultant for Legacy Building Solutions (South Haven, MN). Matt has experience with all aspects of fabric building sales, design-build assistance and project management. He works with end users, contractors and government entities throughout solicitation, development, review and submission. He can be reached at [email protected]. For more information, visit www.legacybuildingsolutions.com.
Note
1. Introduced by Legacy Building Solutions.
2. A new PVC called ExxoTec™ was introduced by Legacy Building Solutions a few years ago and is offered for all Legacy fabric buildings. Designed to provide twice the strength of a standard PE fabric, ExxoTec is available at a comparable price point.